Maximizing Precision in Copper CNC Machining for Electronics and Automotive Applications
Copper CNC machining is a significantly popular technique in manufacturing that leverages the exact, computerized capabilities of Computer Numerical Control (CNC) technology to create intricate elements from copper. CNC machining permits for complex geometries that would certainly be hard or impossible to achieve with conventional machining strategies, making it perfect for the manufacturing of detailed parts, such as ports, warmth sinks, and housings.The procedure of CNC machining entails the use of a computer to control device tools for a much more trusted and regular output. Specialized tools and techniques are typically used to enhance the machining process, which can consist of utilizing reducing devices covered with difficult materials to lessen wear and enhance performance when working with soft metals like copper.
Discover copper cnc machining exactly how copper CNC machining merges sophisticated innovation with lasting techniques to generate intricate, high-precision components, driving development throughout markets like electronics, automobile, and aerospace.
Amongst the key benefits of CNC machining copper is the capacity to produce complicated shapes that conventional machining methods may not accommodate. The high precision possible via CNC modern technology permits suppliers to develop snugly toleranced attributes that are vital in lots of applications. In the electronic devices market, for example, the demand for components with minimal resistances is vital, as digital gadgets lessen and much more intricate. CNC machining promotes the manufacturing of micro-components with such great resistances, allowing developments in smart tools, wearable modern technology, and various other consumer electronics. Furthermore, the repeatability of the CNC machining process ensures that automation of copper components keeps harmony, hence satisfying rigid market requirements.
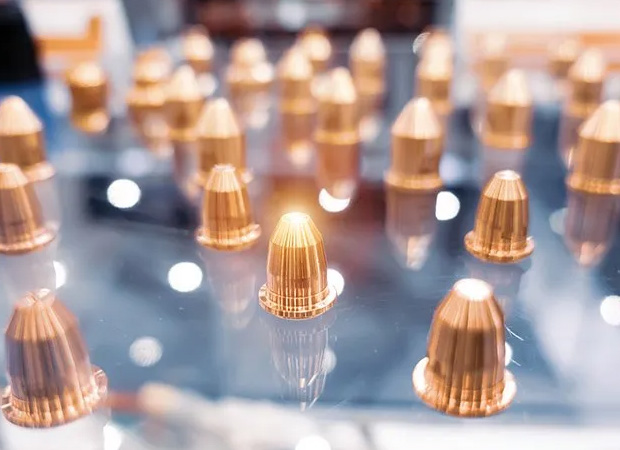
Temperature administration plays a crucial duty in the CNC machining of copper due to its ability to perform warm swiftly. High-speed machining can lead to considerable heat generation, which might adversely impact the residential or commercial properties of the copper and aggravate tool wear.
The sustainability aspect of CNC machining copper is not to be ignored. CNC machining, paired with sustainable methods, can lower waste by allowing producers to use scrap copper from various other processes.
Along with sustainability, cost-effectiveness is one more essential aspect for suppliers choosing CNC machining for copper elements. The first financial investment in CNC machinery may be significant, the long-term benefits can exceed the prices. CNC machining offers a decrease in labor prices as a result of its automated nature and decreases the requirement for substantial hand-operated intervention. The precise control & repeatability provided by CNC innovation minimizes scrap prices, decreasing product costs. Additionally, for small to medium set production runs, CNC machining can prove more economical compared to conventional machining processes, as it enables for smooth changes and style adjustments without considerable retooling. This capacity to pivot quickly can be advantageous, particularly in fast-paced industries where market demands can shift unexpectedly.
Furthermore, as technology evolves, the functionalities within CNC systems are expanding, better boosting the capacities of copper machining. The integration of simulation software permits suppliers to anticipate possible problems prior to the machining process begins. These simulations enable far better preparation of tool paths and elucidate how the copper product will certainly react throughout the machining procedure. By determining and attending to potential obstacles beforehand, business can reduce downtime and increase performance, producing a smoother operational flow.
Education and experience in CNC machining are crucial for recognizing the full possibility of copper processes. Skilled machinists have to be proficient in interpreting layout specs, picking the proper tools, and readjusting machining specifications to reduce concerns related to copper's unique machining attributes. Furthermore, the advancement of additive production technologies, such as 3D printing, has actually produced new standards in the processing of copper. Crossbreed machining, which combines typical CNC machining techniques with additive manufacturing, is arising as a practical approach for creating elaborate copper parts, mixing the strengths of both modern technologies and potentially changing just how producers approach copper manufacturing.
In the world of research and development, CNC machining is helping the expedition of brand-new copper alloys to enhance performance additionally. As worldwide sectors function toward greater energy effectiveness, copper's duty as a conductor in digital circuits will remain critical, driving demand for sophisticated machining remedies.
The aerospace and automotive industries are likewise keen adopters of copper CNC machining, especially where lightweight elements are of important value. As the change towards electrical and hybrid automobiles proceeds, the need for high-performance copper components will likely surge, thereby propelling the demand for advanced CNC machining techniques that make certain performance and top quality in manufacturing.
As CNC machining modern technology remains to establish, it permits further automation, where fundamental processes such as device adjustments, examinations, and upkeep can be configured into the production cycle. This evolution means that manufacturers will certainly have the ability to attain greater efficiency levels, shorter preparations, and better versatility in fitting customized requests or variations in layout. Therefore, services that engage in CNC machining operations are much better matched to pivot in action to the changes in consumer and market demands, cultivating development in a progressively competitive landscape.
Discover countersink size chart how copper CNC machining combines innovative innovation with sustainable practices to generate complex, high-precision elements, driving development throughout sectors like electronics, auto, and aerospace.
The global industry for CNC machining of copper is seeing significant development, affected by aspects such as the rise of wise technologies, electrical vehicles, and continuous efforts to improve energy effectiveness throughout different applications. In this training, advancement and skill advancement continue to be critical; spending in workforce education and learning on CNC machining techniques, advancements, and product sciences will certainly empower makers to stay in advance of the contour.
To conclude, the assimilation of CNC machining with copper materials supplies an unique affordable edge for suppliers in today's fast-paced commercial landscape. Its ability to provide high accuracy, decrease manufacturing time, and enable intricate designs makes CNC machining a necessary component of contemporary manufacturing methods. Paired with sustainability efforts, cost-effectiveness, and possibilities for innovation, the CNC machining of copper not only meets the needs of modern applications but likewise lays the foundation for the future trajectory of manufacturing in several fields. As industries progress and the borders of technology broaden, welcoming CNC machining's potential will certainly be vital to realizing unmatched growth and innovation in the use of copper items. The synergy of copper's material buildings with advanced CNC machining methods proclaims a new age in which accuracy, sustainability, and efficiency work together to develop revolutionary elements that will certainly specify the future of production and beyond.